An assembly line conveyor is a crucial component in manufacturing and production environments. It facilitates the efficient movement of products or parts from one workstation to another, enabling streamlined and continuous assembly processes. Here’s an in-depth look at the components, types, benefits, and considerations for assembly line conveyors:
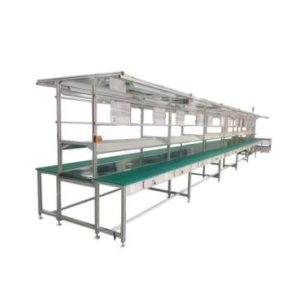
Components
- Conveyor Belt
- Material: Made from rubber, fabric, metal, or plastic, depending on the application.
- Design: Continuous loop that can be flat, cleated, or modular.
- Width and Length: Varies based on the size and type of products being conveyed.
- Frame
- Material: Constructed from aluminum, steel, or stainless steel.
- Design: Provides structural support and can be customized to fit specific layouts.
- Motor and Drive System
- Motor: Powers the movement of the conveyor belt.
- Drive System: Includes gearboxes, chains, or belts to transmit power from the motor to the conveyor belt.
- Rollers
- Material: Typically made from steel or plastic.
- Function: Support the belt and facilitate its movement.
- Leg Supports
- Adjustability: Adjustable in height to ensure the conveyor is level and aligns with other equipment.
- Mobility: Can be equipped with casters for easy movement and repositioning.
- Control System
- PLC (Programmable Logic Controller): Manages the operation of the conveyor, including speed, start/stop functions, and integration with other equipment.
- Sensors: Detect the presence of products and ensure precise control of the conveyor.
- Side Rails and Guards
- Material: Typically made from metal or plastic.
- Function: Prevents products from falling off the sides of the conveyor.
- Accessories
- Workstations: Integrated work areas where specific assembly tasks are performed.
- Tools and Fixtures: Hold products in place and assist workers in the assembly process.
- End Stops and Diverters: Control the flow and direction of products on the conveyor.
Types of Assembly Line Conveyors
- Belt Conveyors
- Description: Uses a continuous loop of material to move products.
- Application: Suitable for a wide range of products and assemblies.
- Advantages: Smooth, continuous movement, and easy to clean.
- Roller Conveyors
- Description: Uses rollers to move products, can be powered or gravity-driven.
- Application: Ideal for heavy or bulky items.
- Advantages: Durable and can handle a wide range of product sizes.
- Chain Conveyors
- Description: Uses chains to move products, often used for heavy loads.
- Application: Common in automotive and heavy machinery assembly.
- Advantages: High load capacity and durable.
- Overhead Conveyors
- Description: Uses a track system to move products above the work area.
- Application: Saves floor space and allows for multi-level assembly.
- Advantages: Efficient use of space and flexible routing.
- Slat Conveyors
- Description: Uses slats attached to a chain to move products.
- Application: Suitable for heavy or sharp items.
- Advantages: Durable and can handle heavy loads.
- Pallet Conveyors
- Description: Uses pallets to move products.
- Application: Suitable for large or heavy items that require stable support.
- Advantages: Provides a stable platform for heavy products.
Benefits
- Efficiency: Streamlines the assembly process, reducing production time.
- Consistency: Ensures consistent movement and positioning of products.
- Flexibility: Can be customized and reconfigured for different products and processes.
- Ergonomics: Reduces the need for manual lifting and carrying, improving worker safety.
- Integration: Easily integrates with other automated systems and equipment.
Design Considerations
- Load Capacity: Ensure the conveyor can handle the weight of the products and parts.
- Speed: Determine the appropriate speed for efficient assembly without causing product damage.
- Layout: Design the conveyor layout to fit the available space and workflow requirements.
- Product Specifications: Consider the size, shape, and weight of the products being assembled.
- Safety: Incorporate safety features such as emergency stop buttons, guards, and sensors.
- Maintenance: Design for easy access to components for maintenance and repair.
- Ergonomics: Ensure the conveyor height and workstation design are ergonomically suitable for workers.
Typical Layouts
- Linear Layout: Products move in a straight line from start to finish.
- U-Shaped Layout: Conveyor forms a U-shape, allowing workers to access multiple stages from a central area.
- Circular Layout: Conveyor forms a loop, often used for continuous or cyclic processes.
- Z-Shaped Layout: Conveyor has multiple changes in direction, ideal for complex workflows.